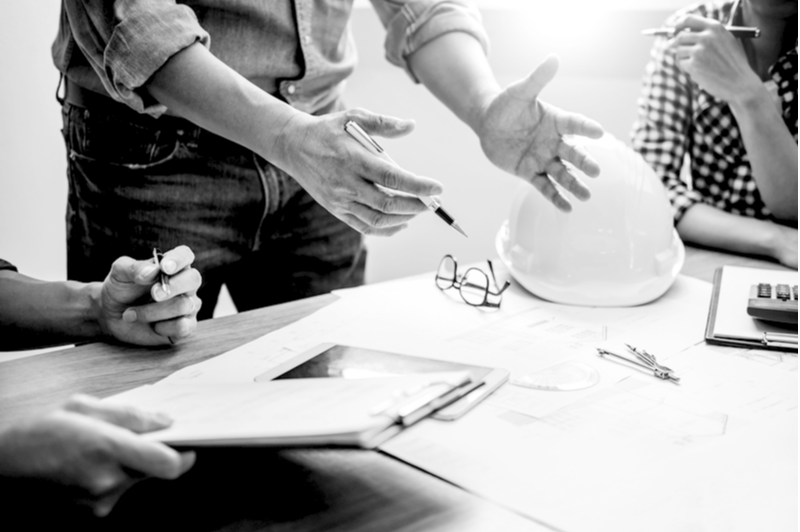
Accidents are inevitable, but lessons learned are valuable tools to help prevent similar accidents from happening in the future. Critical analysis post-accident and implementation of proper safety measures can yield positive results. Reduced accidents can yield a lower workers’ compensation modification, reduced insurance costs, and the ability to competitively bid for more jobs.
The first step in accident analysis is determining the root cause of the incident. Typically, there are four driving factors: People, Equipment, Environment, and Management.
People
Human error is a common denominator contributing to many worksite accidents. In addition to your employees, there are numerous other people that can contribute to an accident including other trades, project managers, laborers, vendors, and more. Often the root cause can be drilled down to the following:
- Lack of procedures
- Procedures not followed
- Procedures not known or understood
- A task is too difficult to perform
- Personal Protective Equipment (PPE) not used or available
- People not trained
- Training inadequate
- Distraction, emotions, or fatigue
Equipment
The utilization of tools and equipment is necessary to perform the requisite work on any project. Most accidents that involve equipment as a leading cause of an accident can be attributed to the following:
- Equipment not maintained
- Wrong equipment used
- Poor equipment design
- Correct equipment not available
Environment
Many environmental elements can contribute to the likelihood of an accident. While forces of nature can not be prevented, preparedness and proper safety measures can reduce the environmental impact on the work site. Some of these triggers include:
- Location of employee
- Temperature extremes
- Poor lighting
- Poor housekeeping
- Inadequate ventilation
- Excessive vibration
- Excessive noise
- Condition of work surface
Management
How a job site is managed is a critical factor that can aid or prevent the possibility of an accident. These Management examples might seem obvious, but unfortunately, poor management can still lead to accidents:
- No management system in place to control hazard
- Supervision did not detect unsafe conditions or behavior
- Supervision did not take action to correct unsafe conditions or behaviors
- Lack of supervisor training
- Lack of accountability for safety
After you determine which of the four areas – People, Equipment, Environment, or Management - the accident circumstances fall within, start asking a series of “why?” questions to determine the reasons for every set of circumstances.
When you have run out of “why?” questions, analyze the results. Eliminate any unlikely causes or circumstances that you cannot control. Then you should be able to identify the accident's cause. Lastly, determine what management system needs to be in place to assure that the accident does not happen again.
A thorough and proper analysis of an accident can reveal a great deal. By identifying the root cause of an accident, you will be able to learn from it and put procedures in place, so similar accidents do not happen in the future. If you have any questions regarding how to properly analyze an accident, reach out to TSIB.
TSIB’s Risk Consultants are currently servicing the following locations:
East Coast: New York City, NY; Bergen County, NJ; Fairfield County, CT; Philadelphia, PA
Texas: Austin, San Antonio, Houston, Dallas
California: Orange County, Los Angeles County, Riverside County, San Bernardino County, San Diego County
image credit: Freedomz/shutterstock.com
Comments